Hightech für Sternengucker
30.11.2022
Kilian Rees hat im Maschinenbaustudium im Labor für Maschinenkonstruktion und Produktentwicklung eine vierachsige Halterung für ein Teleskop konstruiert. Die Vorrichtung erlaubt unter anderem die motorisierte Nachverfolgung von Himmelskörpern.
Nach den Sternen greifen, ist nicht sein Ding. Dazu ist Kilian Rees zu sehr auf dem Boden geblieben. Aber dass der Nachwuchsingenieur alles möglich macht, um Sterne und Galaxien klar und deutlich sichtbar zu machen, hat er in seiner Projektarbeit im Maschinenbaustudium zielstrebig mit enormen Einsatz bewiesen. Er hat eine hochkomplexe parallaktische Montierung konstruiert und gebaut. Dabei handelt es sich um eine stabile Halterung für ein Teleskop, die erlaubt, es für den fokussierten Blick auf Himmelskörper über verschiedene Achsen zu bewegen.
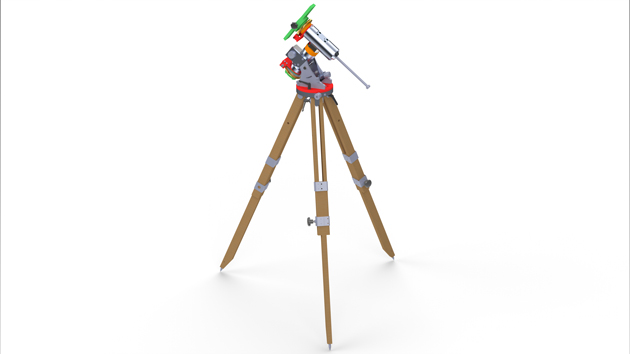
Hobby-Astronom seit der Schulzeit
Eine AG während seiner Gymnasialzeit hatte bei Kilian Rees die Leidenschaft für die Astronomie geweckt. Seitdem wollte er eine solche Montierung besitzen. „Ich hatte bisher nur etwas Billiges, etwas in dieser Ausführung ist richtig teuer. Ein Student kann sich das natürlich nicht leisten.“, sagt Rees mit Blick auf seine Konstruktion. Nun besitzt er eine qualitativ hochwertige Montierung, die er ganz nach seinen Bedürfnissen gestalten konnte. Und nebenbei hat er auch noch viel für sein Studium bzw. das künftige Berufsleben gelernt.
Was ist eigentlich eine parallaktische Montierung?
Ein Teleskop wird verwendet, um nachts Sterne, Galaxien und andere Objekte am Nachthimmel zu beobachten. Über einen Spiegel und mehrere Linsen wird dieser sehr stark vergrößert. Der Vergrößerungsfaktor übersteigt dabei den eines Fernglases um ein Vielfaches. Ein Teleskop jedoch bringt schnell mal mehrere Kilogramm auf die Waage, weshalb die Handhabung sehr einschränkt ist.
Ein solches Gewicht stabil ohne Zittern zu halten und gleichzeitig auf einen Stern zu richten, ist nur mit Händen nicht möglich. Zudem sind die wirklich schönen Nebel und Galaxien mit bloßem Auge zunächst unsichtbar. An dieser Stelle kommt die konstruierte Teleskopmontierung ins Spiel.
Die parallaktische Montierung erlaubt nun, mit ihren verschiedenen Achsen und Getrieben, die feine Ausrichtung des Teleskops je nach Bedarf. Zudem kompensiert sie mit einem eingebauten Schrittmotor die Erdrotation, so dass Himmelsobjekte automatisch nachverfolgt werden. Die besondere Bauart reduziert dabei den erforderlichen Aufwand auf ein Minimum.
So können Astronom*innen die parallaktische Montierung nutzen
„Zuerst wird die Hauptachse am Polarstern ausgerichtet“, erläutert Kilian Rees. Anschließend kann man beliebige Sterne aufsuchen und beobachten. Die Kunst bestehe darin, selbst kleinste Nebel und Galaxien aufzufinden, die mit bloßem Auge unsichtbar sind. Möglich ist dies durch an den Achsen angebrachten Skalen, an denen deren Koordinaten genau eingestellt werden können. Wie auch auf der Erdkugel gibt es am Himmel ein Koordinatensystem bestehend aus einem Gradnetz. Die Position der einzelnen Sterne usw. kann damit genau angegeben werden.
Die parallaktische Montierung erlaubt darüber hinaus, die durch die Erddrehung verursachte scheinbare Bewegung der Gestirne durch Nachführung zu kompensieren. Dadurch kann jedes Himmelsobjekt trotz seiner Bewegung genau im Gesichtsfeld des Teleskops gehalten werden. Damit dies nicht händisch erfolgen muss, hat Kilian Rees die Steuerung für einen Schrittmotor entwickelt, der mittels Batterie betrieben wird.
Eine besonders große Herausforderung war die Konstruktion der Schneckengetriebe, die für den Antrieb zuständig sind. „Es gibt keine einheitliche Vorgehensweise für die Berechnung aufgrund der vielen unbekannten Parameter“. Auch müsse die Zahngeometrie im CAD-Programm exakt nachempfunden werden.
Doch nicht nur die Berechnung der Zahnräder war eine Herausforderung. Auch die Herstellung war vertrackt. „Eine Sonderanfertigung wäre sehr teuer geworden“, erinnert sich Kilian Rees. Die Lösung fand der Student auf dem Campus: Statt mehrere hundert Euro pro Schneckenrad für eine externe Fertigung berappen zu müssen, hat er seine Konstruktion mit einem speziellen 3D-Drucker an der HTWG im OIL ausgedruckt. Dadurch konnten die Kosten um den Faktor 10 reduziert werden sagt Rees. Stereolithografie nennt sich das Verfahren, bei dem mit einem Laser und flüssigem Kunststoff gearbeitet wird. Das ist zugleich auch die besondere Innovation an dieser Montierung betont er.
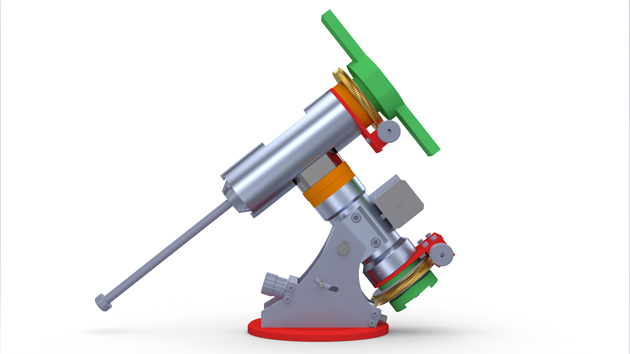
Knowhow der Mitarbeiter der mechanischen Werkstatt
Noch weitere Services der HTWG konnte Kilian Rees nutzen: Allen voran das Knowhow und die Erfahrung der Mitarbeiter der mechanischen Werkstatt. Sie haben seine CAD-Konstruktion geprüft und schließlich auch zum Leben erweckt. Die Fertigung komplexer Teile ist für sie dank modernster Maschinen kein Problem. Die mehrachsige Konstruktion mit all ihren Raffinessen war allerdings auch für sie ein besonderer Auftrag. „Wir freuen uns, dass es funktioniert hat. Dafür waren allerdings viele sehr detaillierte Angaben nötig“, sagt Armin Kerle, „und die eine und andere Nachfrage: Ob eine Aussparung später für eine Mutter benötigt oder eine Passung geändert wird macht einen großen Unterschied in der Anfertigung“, ergänzt Daniel Böhm. Rund 120 Stunden haben sie für das Projekt in der Werkstatt gearbeitet, grob geschätzt. Jürgen Moosmann sagt mit Blick auf Kilian Rees: „Wenn jemand so selbstständig arbeitet, unterstützen wir gerne.“
Noch mehr Stunden steckte Kilian Rees in die Konzeption und Konstruktion. „Das war sehr aufwändig, da sind schon ein paar Wochenenden draufgegangen“, erinnert er sich schmunzelnd. Anerkennend sagt sein Professor Dr. Dr. Kurt Heppler: „Da ist saubere, gut durchdachte und korrekt berechnete Arbeit nötig. Herr Rees hat den Schritt von der virtuellen Konstruktion im Computer zum funktionsfähigen Produkt exzellent vollzogen - Machinenbau wörtlich genommen bringt den größtmöglichen Studienerfolg.“ Jedes Semester ruft Prof. Heppler seine Studierenden im Studiengang Maschinenbau dazu auf, ein Projekt von Anfang bis Ende umzusetzen. Die Projektidee kommt im Labor für Produktentwicklung und Maschinenkonstruktion oft von den Studierenden selbst. Auch ausgefallene Projekte wie ein U-Boot oder eine Currywurst-Maschine wurden bereits realisiert.
Zu guter Letzt: Auch das Stativ hat Kilian Rees selbst gebaut. Bewusst hat er sich für Eschenholz entschieden. „Das Holz dämpft Schwingungen besonders gut“, erläutert er.
Vielfalt des Maschinenbaus
Im Rückblick ist er sehr zufrieden. Es habe Spaß gemacht, ein Projekt von Beginn an bis zum Abschluss durchzuführen. „Es ist eben etwas anderes, ob ich nur ein Einzelteil konstruiere, oder mehrere Teile, die dann zusammenpassen müssen“, sagt Rees. Und es habe Spaß gemacht, die Vielfalt des Maschinenbaus und des Erlernten in dem Projekt anwenden zu können.
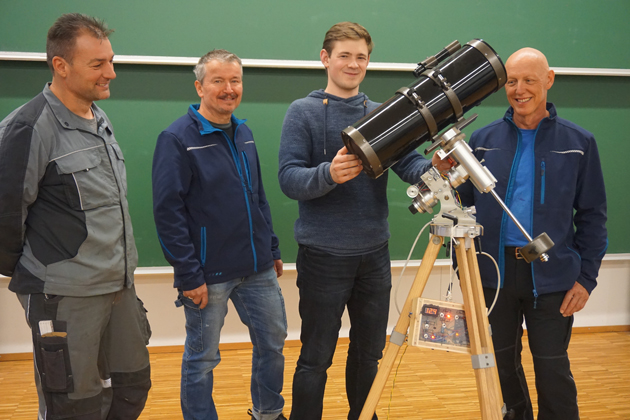